News Summary
Ajax Paving of Florida has enhanced its operational efficiency by integrating advanced construction management software, B2W. This software optimizes work orders, inventory management, and scheduling while reducing costs and time. The company now utilizes real-time insights for parts management, streamlined procurement, and improved inventory management, resulting in a significant decrease in operational inefficiencies. Innovative delivery methods and revised inspection protocols also play a crucial role in Ajax’s commitment to efficiency. These advancements are set to position the company strongly in the competitive construction industry.
Ajax Paving of Florida Boosts Efficiency with Advanced Construction Management Software
Ajax Paving of Florida has recently enhanced its operational efficiency and reduced inventory costs by adopting advanced construction management software known as B2W. This strategic move is set to provide competitive advantages by streamlining various processes within the organization. The adoption of technology has led to noticeable improvements in work orders, parts inventory, and service scheduling, ultimately saving both time and money.
Real-Time Insights Transform Operations
The utilization of construction management software has equipped Ajax Paving with real-time insights into parts ordering and machine issues. Previously, the company faced challenges with recurring parts orders every 90 days, prompting investigations into potential underlying reasons for this pattern. Now, technicians have access to an app that allows them to order parts seamlessly, which then filters through centralized purchasing at the main warehouse. This centralized approach increases efficiency in fulfilling parts requests.
Streamlined Inventory Management
Ajax operates one main warehouse that contains approximately 95% of its inventory, supplemented by smaller inventories at satellite shops to ensure quick access to fast-moving parts. The introduction of digital ordering capabilities has empowered mechanics to submit parts requests directly to vendors, substantially reducing the time spent on procurement processes. Furthermore, the option for mechanics to submit pictures of required parts aids the procurement team in ordering the correct items, minimizing mistakes.
Communication Improvements Drive Efficiency
The enhanced communication resulting from the software minimizes inefficiencies, resulting in fewer wrong parts orders. Ajax Paving now sends mechanics to inspect repair requests only when insufficient information is available, reducing unnecessary travel time. Technicians appreciate the app for providing quick feedback on part orders and their statuses, including whether orders are in transit.
Innovative Parts Delivery System
In another leap forward, Ajax has introduced an Uber Eats-style delivery option for parts, which allows couriers to deliver necessary items directly to job sites. This innovative approach replaces the traditional parts runner model, further streamlining operations. Historically, Ajax had faced issues with overstocking parts due to concerns about potential shortages, prompting a re-evaluation of its parts inventory strategies.
Significant Cost Reductions Achieved
A thorough review of current inventory levels resulted in a notable reduction of $100,000, bringing the total inventory down from approximately $500,000. This reduction does not compromise the number of available line items, showcasing that effective inventory management can indeed coexist with lower total inventory costs. Improved availability of parts has contributed to a shorter time frame for closing out work orders, enhancing overall efficiency.
Focused Approach to Parts Delivery
Ajax has further concentrated on the lead times for parts delivery by determining which items to keep on the shelves based on their availability. The introduction of a ranking system prioritizes critical parts essential for operations, ensuring that mechanics have what they need without unnecessary delays. Enhanced visibility into operations allows for better scheduling and reporting accessible across the company.
Transparent Access to Maintenance Reports
Preventative maintenance (PM) reports can now be accessed by all relevant personnel, greatly reducing the dependency on single individuals for data management. The improved systems have effectively streamlined operations and enhanced access to vital information, leading to significant advancements in operational efficiency.
Overall, Ajax Paving of Florida’s adoption of advanced construction management software marks a transformative step toward optimizing their operations, demonstrating the profound impact of technology on the construction industry.
Deeper Dive: News & Info About This Topic
Additional Resources
- Construction Equipment: Ajax Paving Software
- Wikipedia: Construction Management
- PR Newswire: Murphy Tractor and Trimble
- Google Search: Construction Management Software
- Minute Hack: Digital Transformation in Heavy Equipment
- Encyclopedia Britannica: Construction Technology
- For Construction Pros: Leica Geosystems AI System
- Google News: Construction Technology
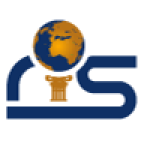
Author: Construction CA News
CALIFORNIA STAFF WRITER The CALIFORNIA STAFF WRITER represents the experienced team at constructioncanews.com, your go-to source for actionable local news and information in California and beyond. Specializing in "news you can use," we cover essential topics like product reviews for personal and business needs, local business directories, politics, real estate trends, neighborhood insights, and state news affecting the area—with deep expertise drawn from years of dedicated reporting and strong community input, including local press releases and business updates. We deliver top reporting on high-value events such as the Rose Parade, Coachella, Comic-Con, and the California State Fair. Our coverage extends to key organizations like the California Building Industry Association and Associated General Contractors of California, plus leading businesses in technology and entertainment that power the local economy such as Apple and Alphabet. As part of the broader network, including constructionnynews.com, constructiontxnews.com, and constructionflnews.com, we provide comprehensive, credible insights into the dynamic landscape across multiple states.